Intelligent Packing Solutions with Scalable Spectral Packing (SSP)
Many industries face common challenges in packing—maximizing space usage while minimizing waste, reducing shipping costs, optimizing packaging inventory, or complying with sustainability and safety regulations. “These 3D packing challenges” are particularly significant in logistics, e-commerce, packaging, and manufacturing. Traditional methods rely on manual processes and simple algorithms, often resulting in inefficiencies and higher costs. Inkbit’s Scalable Spectral Packing (SSP) offers a new approach to solving these problems. Partnering with organizations, Inkbit develops advanced software solutions that solve 3D packing, cartonization, and digital design challenges.
How SSP Works
The core of Scalable Spectral Packing (SSP) lies in transforming the traditional 3D packing problem from a geometric to a spectral representation. By converting spatial data into a spectral format, SSP leverages Fast Fourier Transform (FFT) algorithms and Graphical Processing Unit (GPU) compute hardware for high-speed calculations. This approach enables the quick analysis and optimization of packing configurations.
Benefits of SSP
- SSP stands out for its ability to quickly identify optimal packing configurations, surpassing the capabilities of manual or traditional computational approaches. This means you can achieve efficient packing solutions in a fraction of the time. The technology also excels in packing density, allowing for more items to be packed in less space, which leads to significant reductions in shipping and packaging costs.
- The impact of SSP on business operations is clear: shipping costs can be reduced by as much as 15%, and packaging costs by up to 10%. Beyond cost savings, SSP streamlines design workflows, improves process efficiency, and supports sustainability goals by minimizing material waste.
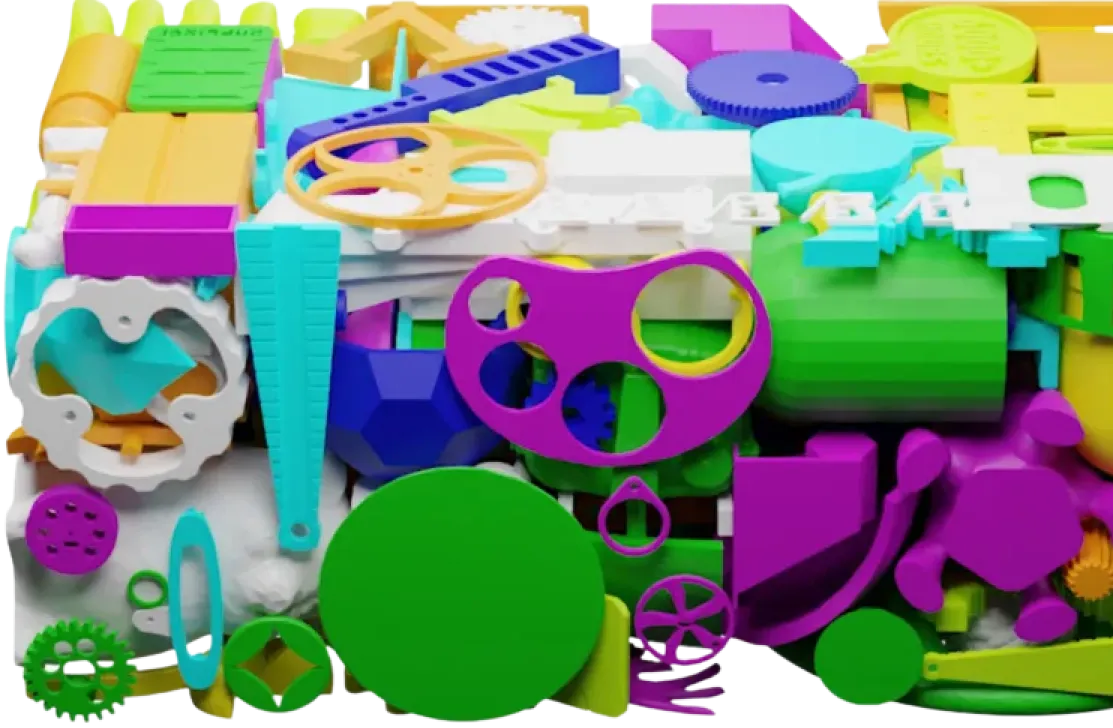

packaging
design
Reducing the time required to validate and develop new packaging designs.
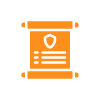
regulatory compliance
Addressing requirements like the European Union’s Packaging and Packaging Waste Regulation (PPWR)
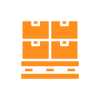
inventory & cartonization
Providing real-time box sizing and inventory optimization to minimize unused space.
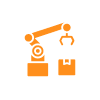
fulfillment operations & robotics
Enabling efficient use of space in automated fulfillment systems.
Case Studies
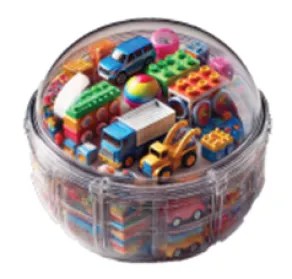
Global Candy company streamlines packaging design
A global candy company that designs approximately 400 toys and over 1.2 billon pieces annually faced a labor-intensive process to validate each design for packability and safety. This process resulted in extended design cycles and higher costs.
Inkbit’s SSP technology digitized the validation workflow, reducing the design cycle from weeks to days. This solution reduced both the time and cost associated with manual checks while improving the overall efficiency of the packaging design process.
Outcome: Fast design iteration, cost savings, and increase safety and regulatory compliance.
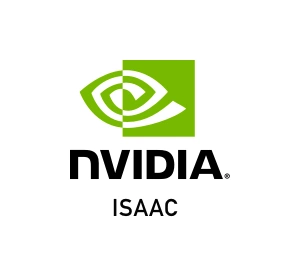
Real-Time Box Selection for E-Commerce with Global Packing Equipment company
IMA, a company specializing in packaging machinery, needed a solution for producing boxes in a variety of sizes to efficiently pack and ship different items. Their goal was to select the optimal box for each order to minimize shipping and packaging costs while ensuring compliance with EU regulations, which limit empty space in e-commerce packaging to a maximum of 50%.
By integrating Inkbit’s SSP real-time API, IMA gained the ability to dynamically choose the most efficient box size for each order. This optimization minimized unused space, reduced packaging material usage, and lowered shipping expenses, all while meeting regulatory requirements.
Outcome: In SSP benchmarks the company achieved a 15% reduction in shipping costs which will lead to a 10% decrease in packaging costs, maintaining compliance with packaging standards.
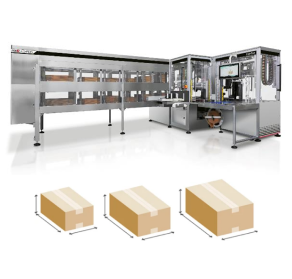
Robotics Fulfillment & Packing Optimization
A leading robotics fulfillment company sought to enhance the performance of their robots. Specifically, they needed software to maximize packing density while taking into account robotic constraints like reachability and collision avoidance.
Inkbit’s SSP solution was integrated with physics-based simulations to optimize robotic packing operations. The technology took into account various factors, including the robot’s limitations and the physical dynamics of items being packed, resulting in increased packing density and improved operational accuracy.
Outcome: Enhanced packing density and pick and place accuracy in automated packing, leading to improved fulfillment performance.
Inkbit’s Scalable Spectral Packing (SSP)
Inkbit’s Scalable Spectral Packing (SSP) technology can address every stage of the packaging lifecycle. Whether you need to improve box design, optimize packaging inventory, or enhance robotic fulfillment, SSP integrates seamlessly with your workflows and systems.
We have active customer projects that span the packaging lifecycle
Packaging Design & Optimization
regulatory compliance
packaging inventory optimization
Cartonization
fulfillment
To Learn More How SSP Can Optimize Your Packing Processes, Contact Us at [email protected]
Additional Resources
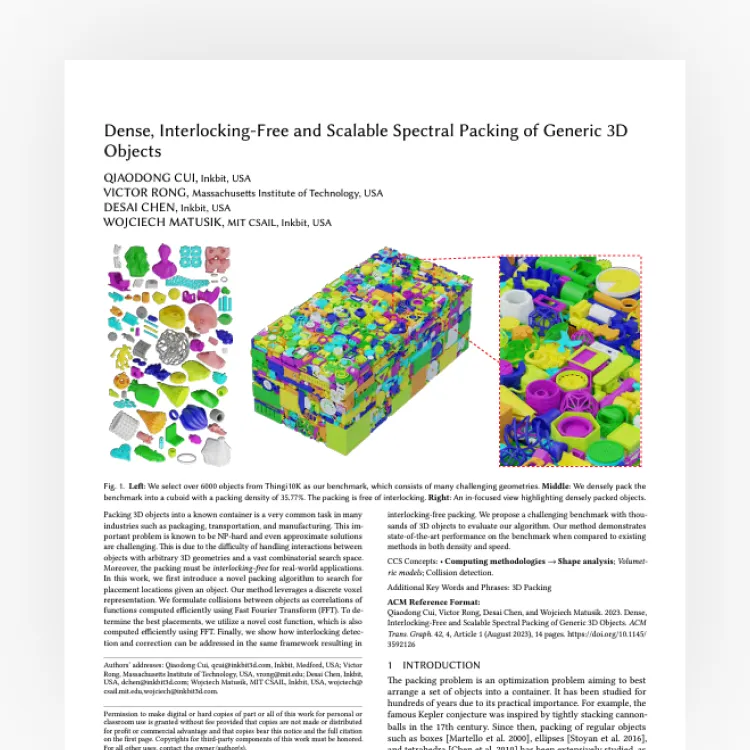
SIGGRAPH Publication
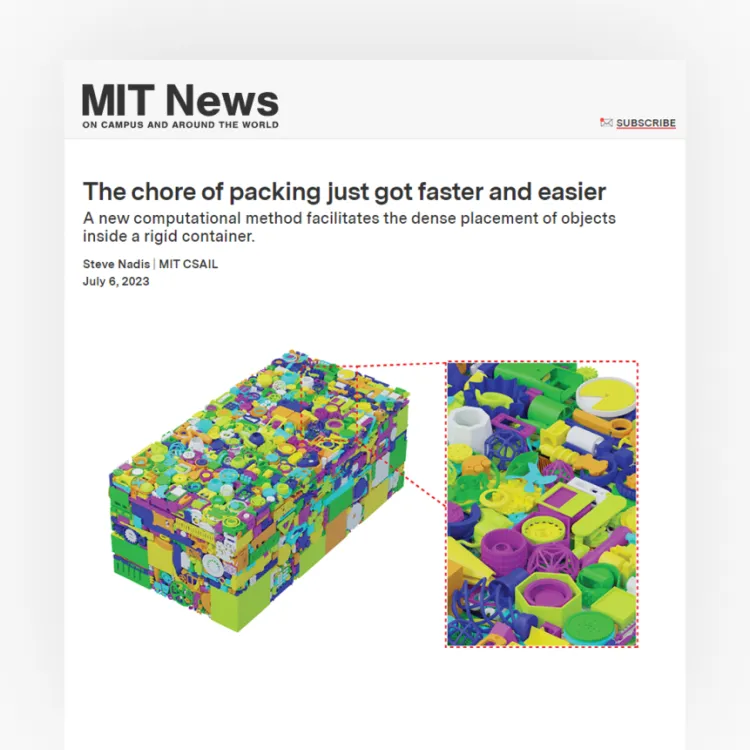
MIT News Article
This work was conducted at Inkbit LLC and is part of Inkbit’s patented and patent pending commercial 3d printing solutions.
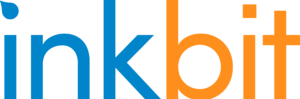
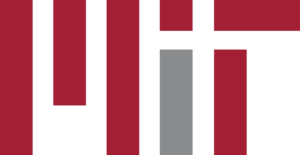